What is Low Value Plastic?
Low Value Plastic (LVP) is any plastic where the costs of collecting and processing the plastic waste are higher than the revenue generated from sales of the recovered plastic. LVP can therefore be any plastic, depending on the geography, but often refers to hard-to-recycle plastics such as Multi-Layered Plastic (MLP), and other soft, flexible plastics. This blog looks at why these plastics are deemed 'low value', why they are hard to recycle, why they are such a challenge in the fight against plastic pollution, and some potential solutions.
What is Low Value Plastic?
Low value plastic is any plastic where the costs of collecting and processing the plastic waste are higher than the revenue generated from the sale of the recovered plastic.
Low value plastic (or LVP) can therefore include variety of plastic types and polymers, but is context specific: what's low value plastic in one area, might have value in another.
Often, what is referred to as LVP is plastic waste that is universally hard-to-recycle, such as Multi-Layered (or Multi-Laminate) Plastic (MLP), and other soft plastics. This blog looks at why these plastics are deemed 'low value' and why they are such a challenge in the fight against plastic pollution.
.jpeg)
Why are soft plastics hard-to-recycle?
MLP is not designed for recyclability. The inherent strength of MLP as a packaging type is that it has multiple layers of different materials, with different properties. Think of several thin sheets of materials (perhaps including aluminium, plastics, and paper) that are laminated together (MLP can also stand for multi-laminate plastic). This can, for examples, help packaging be lightweight and still keep products fresh. Unfortunately, it also means that it would require an energy-intensive recovery process to separate each layer and turn it back into plastic feedstock (the raw materials used to produce plastics). The cost of the recycling process is more than the value of the materials it produces. That makes it a 'low value' plastic.
Similarly, the cost of collecting, separating and repurposing other soft, flexible plastics often outweighs the value it generates. Like MLP, soft plastics are often created from different types of plastics, used in various combinations. Rather than the meticulous and expensive process of separating out the different types of plastic, these materials are more often ‘downcycled’: turned into lower value products that are not suitable for use as food packaging.
Collection systems for soft plastics are limited
This lack of financial incentive hampers LVP management. Government and municipality recycling schemes are unable to deal with the costs and complexities, and rarely accept these plastics. As a result, the default in many countries is for LVP waste to be landfilled or incinerated. For example, in the UK which has relatively well-developed recycling infrastructure in general, only 6% of soft plastics are recycled. This is a problem, as flexible packaging is the fastest growing plastic packaging category and soft plastic materials make up nearly a quarter of consumer packaging. It's estimated that the average household in the US uses 27kg of plastic films every year.
With growing concern from consumers about plastic waste there is a drive for this scenario to change. In some countries, supermarkets and retailers have stepped into the void to collect and recycle soft plastics, though schemes in Australia and the UK have recently met challenges in terms of transparent reporting of recycling rates.
In other parts of the world, where municipal waste collections are more limited, a mirrored scenario plays out. Plastics that have value for local recyclers are collected, often by informal waste workers, while MLP and other soft plastic is not. Instead uncollected soft plastics are dumped at a convenient local spot, and left to pollute the environment. It's this process that so often leads to waterways becoming choked with plastic waste, and waste washing into the ocean.
To remove LVP from the environment, investment is required to cover costs across the value chain: from collection to end disposal. This is one of the ways that rePurpose Global acts on plastic pollution - funding from brand partners is used to bridge this financial gap. Without the financial incentives that our projects provide, waste collectors would neglect LVP waste, leaving it to end up as pollution. With the incentive, LVP is collected, sorted, transported, and taken to the most appropriate end destination.
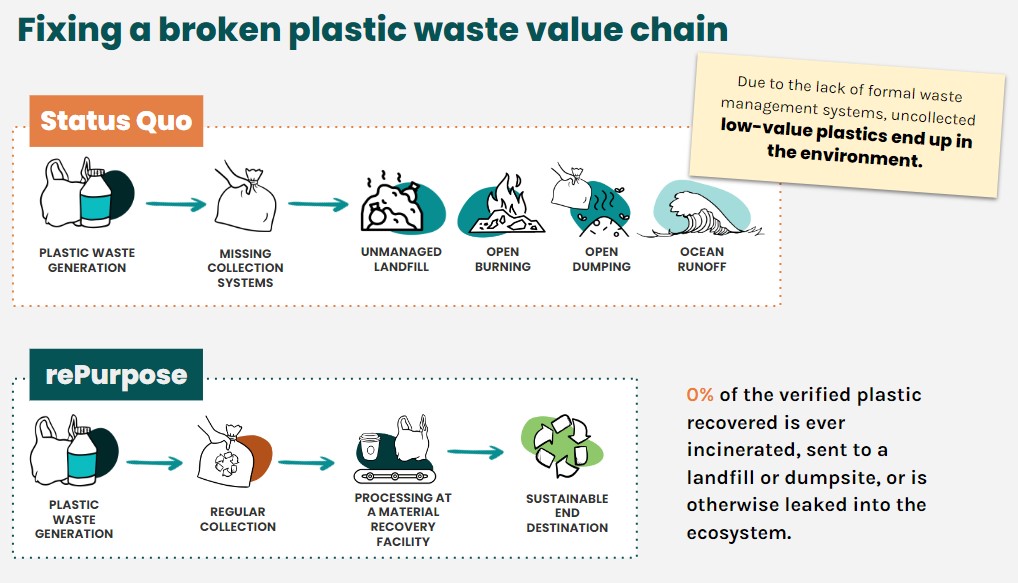
How can we manage low value plastic waste?
What's most appropriate end-of-life destination for LVP? The short answer is: it depends. Since LVP is can be any plastic that is unprofitable to process, the realities and economics of local value chains determine what is classified as LVP, and the best management options for LVP waste.
LVP can include widely recycled plastics such as PET (the plastic used in most plastic drinks bottles) in some circumstances. In Ghana for example, the lack of recycling infrastructure for PET means there is no market for its collection, and no value assigned to the waste. rePurpose Global's impact project Fann Epo in Accra, Ghana, therefore changes this by incentivizing the collection of PET, and providing the finance to transport collected PET for recycling elsewhere (until a local recycling facility is constructed).
As covered above, typically LVP refers to soft plastic and MLP. While technically recyclable, the challenge is that the recycling process to convert materials back to their constituent plastics is complex, expensive, and energy intensive. Where the infrastructure is available, an alternative is to upcycle it into 'plastic wood' (otherwise known as recycled plastic lumber or eco-wood). This involves cleaning and shredding soft plastics, and then heating and extruding the melted plastic into a mould. These moulds can be in the shape of wooden planks, boards, or beams. The resulting plastic wood can be used for flexible, weather resistant building materials as seen below at rePurpose's impact project Sueño Azul, where the materials has been used to construct housing for waste workers.
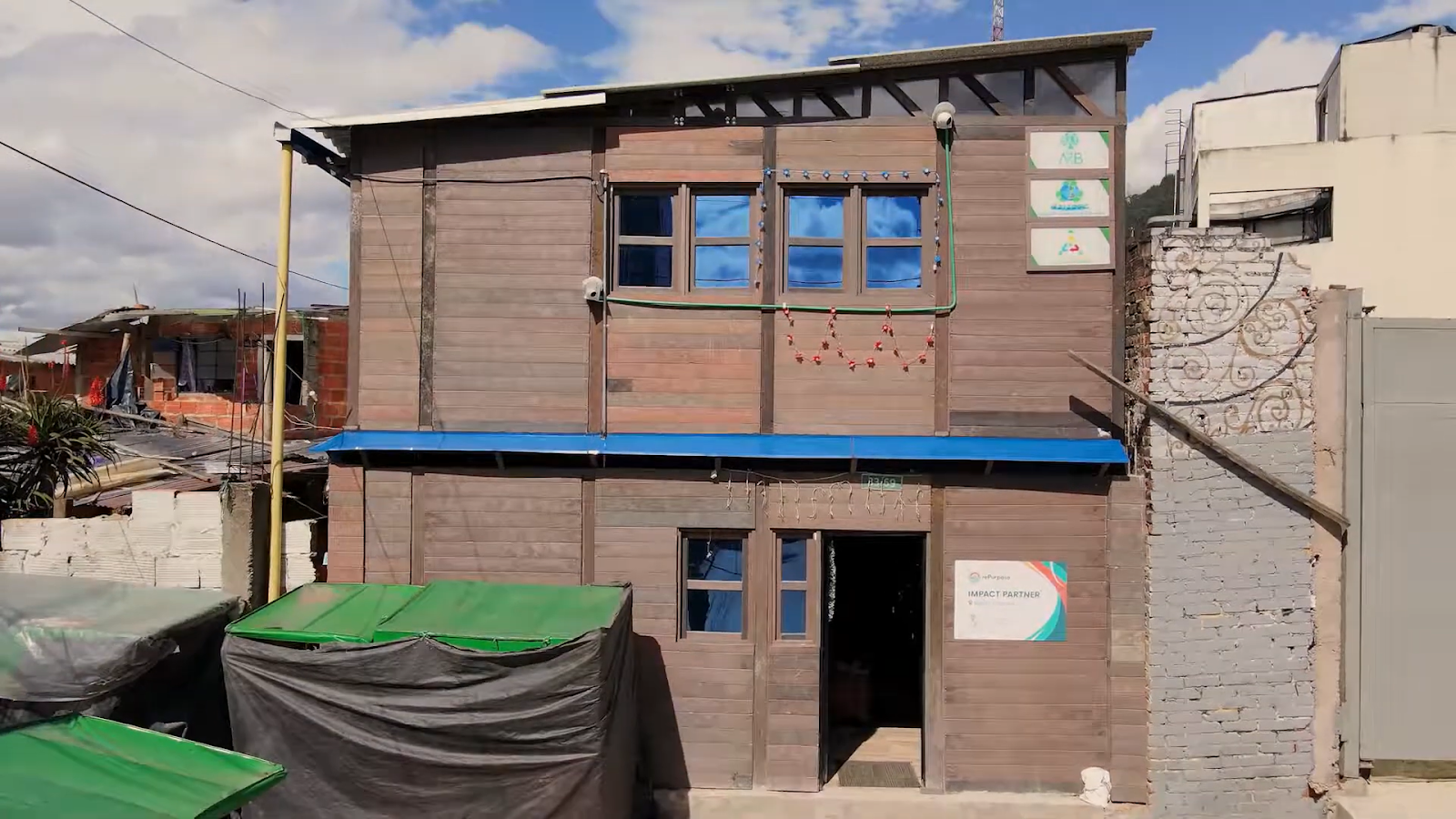
In other parts of the world where this infrastructure is not yet available, a good solution for LVP is for it to be sent for co-processing: replacing fossil fuels in cement kilns. This generates some value for LVP, and - since extremely high temperatures almost completely destroy the plastic (while residual ash can be used in the cement) and the process neutralizes harmful gases - this is recognized by UNEP as a practical, cost-effective, and environmentally preferred option to landfilling or incineration in areas lacking recycling or upcycling facilities.
The future of Low Value Plastics
Innovations that tackle LVP and increase recycling rates and circular uses are helpful in addressing the waste problem and preventing pollution. But innovation is also required to reduce the amount of MLP and other soft plastic waste that are being created: to stop creating the problem in the first place.
There are calls to ban some single-use plastics as part of the UN Global Plastic Treaty, but this is unlikely to extend to all soft plastics and MLP given their prevalence in food packaging and utility in keeping food fresh. On top of that, the overall environmental impact of using plastic packaging, versus alternatives including glass and aluminium, is not clear cut. There are also issues compostable packaging - not least that most of it will not end up being composted. There have, nevertheless, been efforts from some brands to embrace reusable and refillable packaging, or switch away from soft plastic packaging. Further regulation, and the introduction of Extended Producer Responsibility (EPR) schemes will hopefully accelerate this movement.
Low Value Plastic such as soft and flexible plastics will continue to be useful, lightweight, and cheap packaging materials. But they will also continue to be a major source of pollution unless action is taken to reduce their production and use, and find ways to manage the waste that's produced.
-
For more information about rePurpose Global's impact on plastic collection and recovery, please see repurpose.global/impact
Get Started with Verified Plastic Recovery for your Brand
rePurpose Global is here to support your sustainability roadmap with impactful and measurable Plastic Action solutions that deliver immediate results. Partner with us to measure your plastic footprint, fund plastic waste recovery, and create strong sustainability messaging for your brand.
Talk to our team to explore how we can work together.
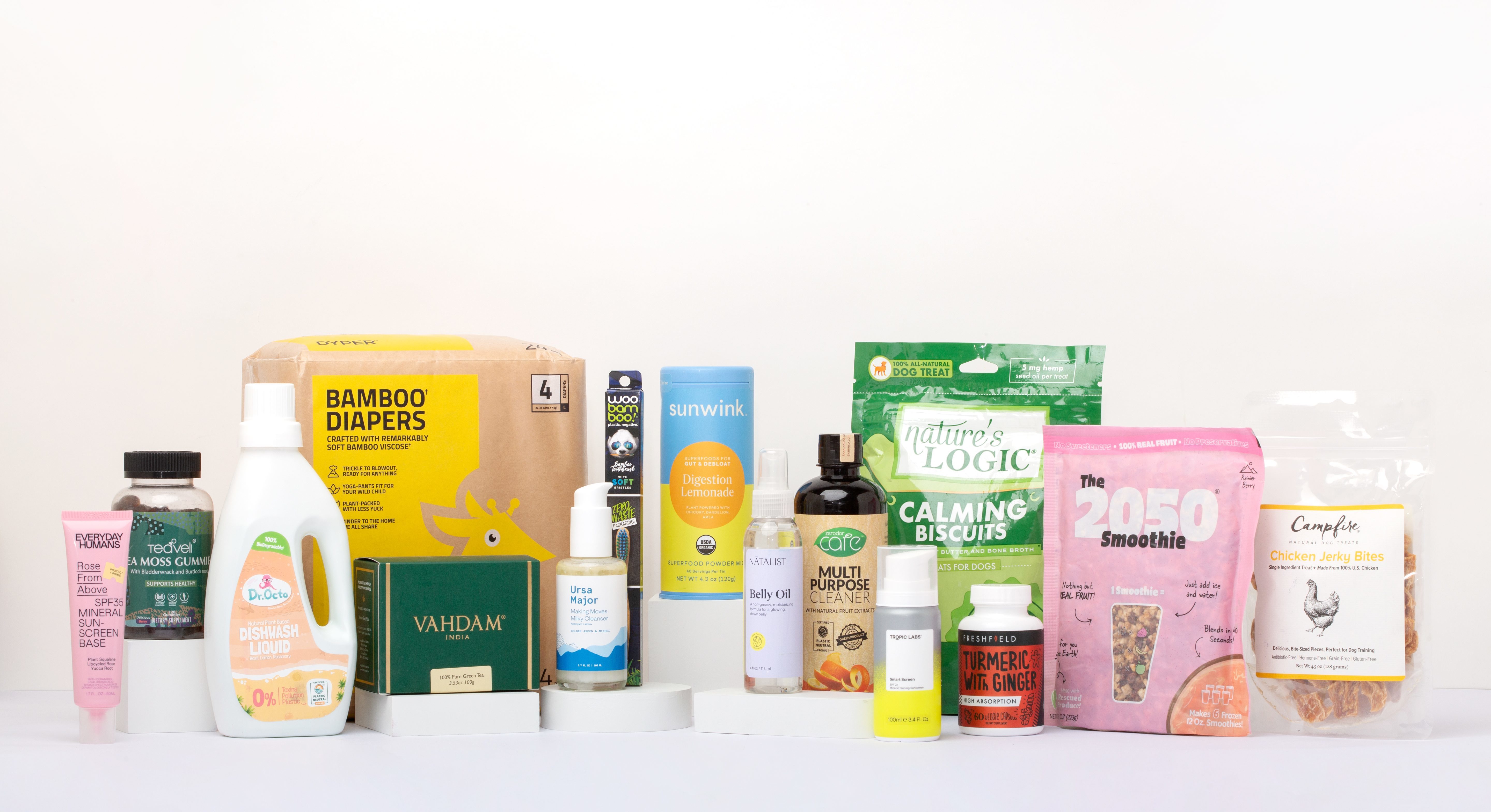
Related Posts
US Waste Exporting Explained
What’s the dark side of waste processing? Learn more about how the plastic products and packagings used by you affect someone on the other side of the world.
6 Eco-friendly Clothing Brands for Your Next Adventure
With consumers becoming increasingly wary of fast fashion brands’ greenwashing, these 6 eco-friendly clothing brands are setting the trend!
The Dangers of Greenwashing in Advertising
Often, environmentally-conscious consumers pay a premium for sustainable goods, hoping that the missions purported by businesses mean we, as individuals, are taking individual steps towards a better future. But, are those ads true or just greenwashing?